Their Cape Cod Home Isn’t Small, but Its Carbon Footprint Is
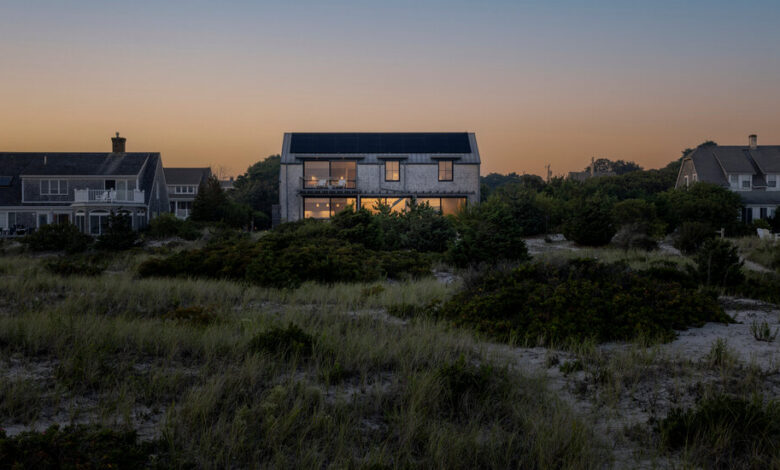
When Michael and Jennifer Monteiro bought a house on Cape Cod, they wanted more than just a vacation home near the beach in Massachusetts: They were determined to own something that reflected cutting-edge sustainability.
Since selling the software company he co-founded, Buildium, in 2019, Mr. Monteiro, 51, has used his investment company, Mpactful Ventures, to focus on projects targeting climate change. And his own home offered an obvious chance to set an example.
As he put it, “Sustainable building is one of the key solutions to the climate problem.”
He and Ms. Monteiro, 47, live in Hingham, Mass., outside Boston, with their children, Maddy, 14, and Jack, 12. After buying a second home as an escape in 2019 — a 1980s oceanfront house in the town of Harwich for $2.6 million — Mr. Monteiro began thinking about how he could renovate to make it more energy efficient.
As he dug in, he uncovered some problems: The house had been poorly built, which made him wonder whether it was worth investing in upgrades, and although it wasn’t in a flood zone, he worried about how rising sea levels might affect it in the future.
“We wanted a house that would be around for a hundred years or more,” Mr. Monteiro said. “But that’s daunting when you think about how the world is changing in the context of climate change.”
The solution, the couple decided, was to demolish the house and start fresh.
Demolition, however, comes with its own environmental concerns. So they began by bringing in GreenGoat, a nonprofit building-material reuse organization to salvage everything worth keeping, and recycled as much of the rest as possible. And they hired Estes Twombly & Titrington Architects to design a new structure: a modern, sustainable house disguised as a traditional shingled cottage.
“Michael mentioned potentially using passive-house design,” said Adam Titrington, a partner at the firm. “But we certainly didn’t know how deep that interest would ultimately become.”
As they began designing, Mr. Monteiro questioned nearly every conventional building material and method proposed, hoping to reduce associated greenhouse gas emissions while also making choices that were good for human health.
Many new houses are tightly insulated with spray foam for energy efficiency, but Mr. Monteiro was wary of the petroleum-based chemicals in those products. So when Kiko Thébaud, a friend who is an architect, told him about hemp-based insulation used in France, he was intrigued.
“It’s called hempcrete or hemp-lime,” Mr. Monteiro said. “It’s hemp hurd, which comes from the woody part of the hemp plant. You use those little pieces mixed with a lime-based binder and then add water, and it creates a slurry that can be sprayed into a wall cavity — like we did — or poured into plywood forms.”
The walls are finished on the outside with lime render; the inside is coated with lime plaster, eliminating the need for wood sheathing, synthetic house wrap, drywall and paint.
The only problem? Spraying is the most efficient way to apply the hemp-lime, but they couldn’t find an American installer with the necessary expertise and equipment. Their solution was to assemble a team of French, Canadian and American specialists and import the spray rig from France.
But that wasn’t enough: Mr. Monteiro and Mr. Titrington also wanted to reduce greenhouse gas emissions related to the production of other materials used in the house. For the concrete foundation, they specified a custom mix with less Portland cement (which generates carbon dioxide during manufacturing) and more fly ash (an industrial byproduct) than would normally be used.
They replaced petroleum-based foam insulation around the foundation with recycled foamed-glass aggregate. For soundproofing some interior walls, they installed HempWool batts. And instead of choosing an exotic hardwood like ipe for the exterior decking, they used locally harvested black locust.
The house is heated and cooled by electric air-source heat pumps, and the solar array on the roof is designed to generate as much energy as the house uses.
The resulting 6,000-square-foot structure isn’t small, but it does have a small carbon footprint. Using the BEAM estimator from Builders for Climate Action, Mr. Titrington determined that the house produces less than half of the carbon dioxide emissions of a conventionally built structure. And in the future, it will be largely self-sufficient.
The Monteiros worked with Liz Stiving-Nichols, of Martha’s Vineyard Interior Design, to furnish the home, choosing renewable, natural materials — cotton, linen, wool, hemp — and avoiding plastics and synthetics. They worked with local manufacturers and craftspeople to produce many of the furnishings, including rugs and sculptural furniture.
The home has a finished basement — currently used for Ping-Pong and shuffleboard — but the walls are removable. That means if flooding becomes a problem in the future, the lower level can be abandoned.
Construction took about two years, because of pandemic-related delays, but the house was complete in July 2022 at a cost of about $1,200 a square foot. Hoping that others may want to follow his example, Mr. Monteiro’s investment company helped fund the US Hemp Building Association’s work to have hemp-lime approved for residential building codes in the United States.
“I don’t expect everybody’s going to want to build with hemp,” he said. “But I hope it causes people to think more about the choices that go into building a house.”
Part of the challenge of finding a more sustainable way to build, he added, is that most people don’t know what’s possible: “As a homeowner, I just didn’t know these opportunities existed.”
Living Small is a biweekly column exploring what it takes to lead a simpler, more sustainable or more compact life.
For weekly email updates on residential real estate news, sign up here.
Source link